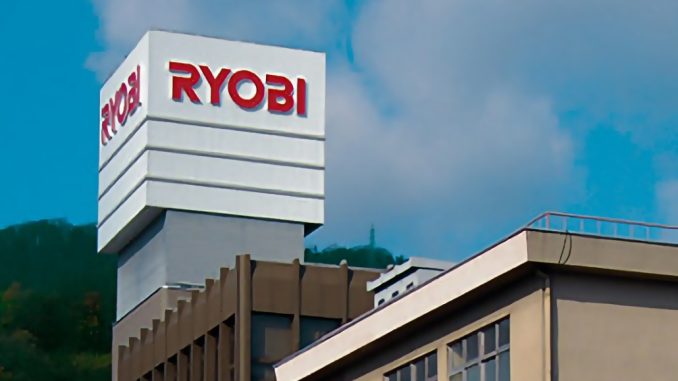
Ryobi, un importante proveedor japonés de autopartes de aluminio, producirá piezas grandes para carrocerías de vehículos eléctricos utilizando «Gigacasting», una tecnología que promete reducir el costo de fabricación de la carrocería de un automóvil en un 20%, dijo el Nikkei.
Ryobi, que está utilizando la tecnología para moldear un gran componente de aluminio diseñado para reemplazar docenas de piezas de acero, se une a una gran cantidad de otros proveedores de autopartes que luchan por transformar sus cadenas de suministro para vehículos eléctricos.
Tesla introdujo Gigacasting en 2020 para reducir los costos de fabricación de vehículos eléctricos, y fue seguido por Xpeng y Zhejiang Geely Holding Group de China. El fabricante de automóviles sueco Volvo Cars y Volkswagen, de Alemania, también tienen planes de presentarlo. Toyota Motor anunció en junio que utilizará la tecnología para que sus vehículos eléctricos se produzcan en masa a partir de 2026.
Toyota planea reemplazar 91 piezas de placas de acero en la parte delantera de las carrocerías de los vehículos eléctricos y 86 piezas de placas de acero en la parte trasera con dos piezas grandes de aluminio.
VIENEN CAMBIOS EN LA CADENA DE SUMINISTROS
La introducción de gigacasting podría eliminar la necesidad de fabricantes de prensas de chapa de acero y generar cambios en la cadena de suministro automotriz. El peso de las piezas de chapa de acero representa el 90 % del peso total de la carrocería de un coche convencional. Munro & Associates, una empresa estadounidense que lleva a cabo desguaces de automóviles, estima que el aluminio representa cerca del 50% de la carrocería de un Tesla.
Gigacasting también puede reducir las emisiones de dióxido de carbono de la fabricación de piezas porque es aluminio reciclado fácil de usar. Las emisiones de CO2 de los productos reciclados son menos de una décima parte de las del aluminio nuevo, que requiere una gran cantidad de electricidad para su producción. Además, el aluminio es un 60 % más ligero y puede mejorar la eficiencia del consumo de energía durante la conducción.
Sin embargo, el gigacasting es difícil de dominar, especialmente la experiencia necesaria para evitar que se formen cavidades cuando el aluminio fundido se vierte en formas complejas. Otra desventaja es la necesidad de reemplazar un componente enorme completo después de una colisión u otros accidentes. (RI/NI/)
Descubre más desde International Press - Noticias de Japón en español
Suscríbete y recibe las últimas entradas en tu correo electrónico.